EnableX Materials for Compression Molding
Traditional ways of fabricating prepreg into shapes is time consuming and expensive. Therefore, the full advantages that a continuous fiber reinforced composite can bring to an application were limited to those specific applications where production volumes were low, and costs were not the overriding concern.
While no material is 100% predictable in any new design, continuous fiber composites are the most predictable type of composite material. Why? Because the fiber orientation can be known, and controlled. Unlike molding compounds, continuous fiber materials do not have flow or knit lines.
One way to make composites workable in large volumes is to machine parts from sheets or other stock shapes such as tubes or rods. These stock removal techniques can create intricate geometries, and do so with moderately high throughput. However, these techniques limit the design flexibility because the fiber orientation is fixed in the shape. And, stock removal techniques can generate too much material loss to be economically viable in some cases.
So, how can the advantages of continuous fiber reinforced materials be matched up with the demands of industry today? Through our own solution: EnableX prepreg materials optimized for compression molding.
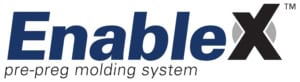
Designed to make composites predictable, scalable, and affordable.
Watch our Free Webinar
Topics Covered Include:
- How composites are designed and built
- Differences between continuous fiber and discontinuous fiber reinforced materials
- How continuous fiber prepreg can be predictable, scalable and affordable
- Considerations how these materials can be engineered for application requirements
EnableX ™ is a prepreg molding system.
EnableX™ is a breakthrough compression molding system from Norplex-Micarta that allows continuous fiber prepreg to be co-cured in a multi-material molding system to produce near net shapes. Building upon the predictability of continuous fiber reinforced prepreg, EnableX™ materials are:
- Specifically designed for compression molding
- Tested to ensure compatibility
- Supported by our team of application engineers
Additionally, like all Norplex-Micarta materials, our in-house laboratory and development capabilities allow for new concepts to be prototyped, or specific datasets to be developed to support specific design criteria.
And the EnableX™ compression molding system is available on a variety of reinforcement fibers and constructions.
EnableX ™ Case Study
The addition of continuous fiber reinforced prepreg has a significant effect on the load bearing capacity of a composite part.
The part was originally manufactured entirely from epoxy molding compound. It was redesigned with a combination of molding compound and continuous fiber prepreg. Both material options yield a part of equal weight, but most notably, the thickness varies in the bridge section, with prepreg reduced the thickness by 0.040″.
Despite this difference in the thickness of the bridge section, the redesigned part utilizing prepreg showed a significant increase in the flexural performance, max load at failure, and deflection at failure (see chart). In the redesigned prepreg part, total failure (complete fiber break) was not observed, but a delamination of the molding compound from prepreg did occur.
EnableX ™ Case Study
Features common in plastic design excel in minimizing deflection in composite parts.
The combination of prepreg and molding compound opens options for designing geometrically complex parts. The addition of ribs in the domed part produces a part with nonuniform deflection behavior. A load placed directly on top of a rib produces less deflection (1/4 inch deflection) than if the load is placed between the ribs (1/2 inch deflection). While this behavior is expected, the degree by which it was manifest in this case demonstrates the significance of using geometry to alter the deflection of a part.
The use of molding compound allows for the creation of detailed features (such as ribs) that open the designer’s window for changing the moment of inertia – using very little material, and therefore adding minimal mass, to dramatically affect deflection.
Collaborative Design Approach
Norplex-Micarta welcomes the opportunity to work with composite design veterans and those new to working with composites. We follow your lead and adapt our development approach to match your timeline and budget.
Generally, the first step is to determine the appropriate resin matrix. The EnableX™ compression molding system has been verified on several different epoxy and phenolic resin systems, and more are always in development. Many of these materials have been tested and can serve as a baseline for virtual modeling. Moreover, these materials are readily available to accelerate the design timeline through physical prototyping.
Reinforcement options for the EnableX™ compression molding system are essentially limitless. From Carbon, to Glass, to natural fibers such as Cotton or Paper, and then to fibers that significantly alter the behavior of the material such as PTFE or thermoplastics, are available in the EnableX™ system. Beyond the fibers themselves, different architectures and hybridizations of reinforcements further expand the design window.
Downloadable Product Literature
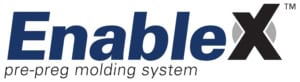